Ball Joints
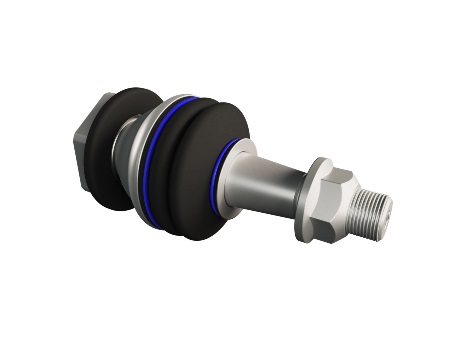
- Product Information
- Product Resources
- Enquire
- Related Products
- Manufactured to OE standards for control, comfort and durability
- Ball-pin 100% crack tested for flaw free material
- Undergo rigorous performance and resilience tests
- Chloroprene rubber cover protects internal components
- Superior ball-pin finish and nylon seat coating for smooth movement and long lifetime
- High specification grease for reduced friction, and smooth operation in all temperatures and conditions
- Cataphoretic coating where required provides longer lasting corrosion protection
- Access to technical hotline and support
- Three-year/36,000-mile warranty on all steering parts – available in UK only
Precision engineering
Enabling free movement in two planes at the same time, the ball-pin is a critical component. That’s why our ball-pins are manufactured from high-grade steel and machined to micron tolerances. Together with a polyoxymethylene nylon ball-pin seat, they provide optimum durability and smooth joint operation.

Extensive testing
Delphi ball joints undergo rigorous performance tests including angular stress testing, where the ball is rotated through its angular and rotational travel under load, as well as a pull and push out test, to measure the force required for it to break away from the housing. These important safety tests ensure the ball joint can withstand the same forces as the OE part.
Longer service intervals
We provide a range of sealed ball joints, that are lubed for life with a high-specification grease, to minimise maintenance requirements. Alongside our precision ball-pin finish and improved rubber boot design, they offer longer ball joint service intervals and better grease retention.
Greater protection
To help prevent damage to the joint’s internal components, all our ball joints come with a special chloroprene rubber cover. The new and improved formula maintains its durability even in extreme temperatures, providing added protection from road dirt or salt and allowing continued free movement of the ball joint for a longer lasting part.
.jpg?sfvrsn=d5e08686_1)
Three-year warranty – available in UK
As a guarantee of our OE-quality standards, we offer a three-year or 36,000-mile warranty on all our ball joints. So, you can fit Delphi steering parts with complete confidence.

Cataphoretic coating
Like many of our steering parts, Delphi ball joints feature an environmentally friendly cataphoretic coating for tougher and longer lasting protection from corrosion caused by salt, dirt and water and other contaminants.
Tech Tip
Delphi is advising technicians to help ensure a quality steering and suspension repair by replacing the entire ball joint component where the rubber boot is split, cracked, damaged or missing. In these instances, there is a high probability that damage to the ball joint may have occurred, indicating the joint is likely to fail even after the boot cover has been replaced. Replacing the entire ball joint component can help avoid potential premature failure, which can be safety-critical and costly.
.jpg?sfvrsn=43ce0fa5_0)
The Delphi Difference
-
100 years of OE experience, supplier to the world’s top automakers
-
OE heritage and knowledge built into every aftermarket part
-
Comprehensive portfolio for a wide range of vehicles and model years
-
Streamlined SKUs for easy inventory management
-
Support through tools, tips and training
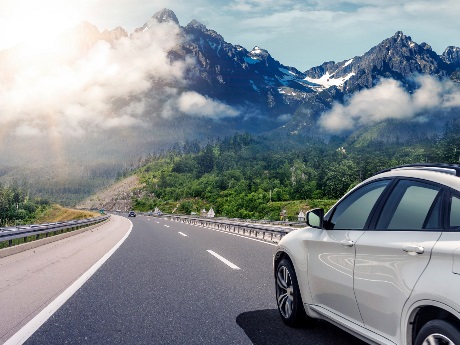
Related product resources and downloads
.tmb-1920w.jpg?Culture=en-GB&sfvrsn=5978f089_5)
Resource Highlights
In this article, we provide a breakdown of what meant by Suspension by taking a closer look at Non-independent suspension, MacPherson Strut Suspension, Double Wishbones Suspension, Torsion Beam Suspension and more.
What is suspension? | Suspension is the term given to the system of springs, shock absorbers and linkages that connects a vehicle to its wheels and allows relative motion between the two. Suspension systems serve a dual purpose — contributing to the vehicle's handling and braking for good active safety and driving pleasure, and keeping vehicle occupants comfortable and reasonably well isolated from road noise, bumps, and vibrations. It is important for the suspension to keep the road wheel in contact with the road surface as much as possible, because all the forces acting on the vehicle do so through the contact patches of the tires. The suspension also helps protect the vehicle itself and any cargo or luggage from damage and wear. The design of front and rear suspension of a car may be different. Below is a description of the most popular types of suspension. |
Non-independent suspension | Basically, non-independent suspension is a rigid axle fixed between left and right wheels. The car body is suspended by leaf springs or coil springs on the axle / wheels unit. The wheels are not independent. When one wheel rides on a hump, the shock will be transferred to another wheel. Both wheels will be cambered, thus non-neutral steering is inevitable. Today this is not very popular for passenger cars due to questionable performance. This type of suspension is used mainly on rear axle vehicles. |
MacPherson Strut Suspension | The MacPherson strut suspension was invented in the 1940s by Earl S. MacPherson. It’s one of the dominating suspensions systems of the world today because of its compactness and low cost. Unlike other suspension designs, in MacPherson strut suspension, the telescopic shock absorber also serves as a link to control the position of the wheel. Therefore it saves the upper control arm. Since the strut is vertically positioned, the whole suspension is very compact. To front-wheel drive cars, whose engine and transmission are all located inside the front compartment, they need front suspensions which engage very little width of the car. The MacPherson strut suspension has challenges, as the body roll and wheel movement can lead to variation in camber. Its relatively high overall height requires a higher hood and fender line, which is not desirable to sports car styling. MacPherson strut can be adopted in both front and rear wheels. |
Double Wishbones Suspension | Double wishbones suspension can be used in front and rear wheels, and as it is independent of one another, it has near perfect camber control. For 40 years and even today, this is the first choice for racing cars, sports cars and luxury sedans. Double wishbones suspension maintains the wheel perpendicular to the road surface, irrespective of the wheel's movement. This helps ensure good handling. Traditional double wishbones suspension consists of two parallel wishbone arms of equal length, which can cause excessive tire scrubbing because of the large variation in track width as the wheel moves off the neutral position. Therefore engineers developed unequal length, non-parallel A-arms to solve this. By tilting the upper A-arm, anti-dive function is also achieved. Double wishbones suspension has been very popular in American cars. European cars are smaller, however, and thus cannot accommodate this relatively space-engaging suspension. Double wishbone suspension is traditionally more expensive than the MacPherson strut and torsion beam because it involves more components and more suspension pick up points in the car body. Very few small cars adopt it, but today due to double wishbone performance, many European compact and D class cars are equipped with this system in front and rear suspension. |
Torsion Beam Suspension | Most modern mini-cars up to C-segment employ torsion beam as the rear suspension. Compared to double wishbones, multi-link and trailing arm suspensions, it engages little width of the car, thus enabling greater rear seat room. It is cheaper too. Compared to the MacPherson strut, its shock absorber is shorter and can be inclined steeply away from the vertical, thus taking up less trunk space. The torsion beam suspension is only half-independent - there is a torsion beam connecting both wheels together, which allows limited degree of freedom when forced. For some less demanding compact cars, this saves the anti-roll bars. It does not provide, however, the same level of ride and handling as double wishbones or multi-link suspensions. Most of Europe's best handling GTIs employed this suspension. |
Multi-link Rear Suspension | Since the late 80s, multi-link rear suspension is increasingly used in modern sedans and coupes. It is difficult to describe its construction because it is not strictly defined. In theory, any independent suspensions having three control arms or more are multi-link. Different designs may have very different geometry and characteristics. It is a relatively space-engaging system, but offers very good handling. Some multi-link models are essentially a double wishbones suspension added with the fifth control arm. It looks like the double wishbone design, but eliminates torque steer. Most sports cars and all the best racing cars still use double wishbones. |
Trailing and Semi-trailing Arm Suspension | Trailing arm and semi-trailing arm suspensions are rather old. This style was commonly used in nearly all mid-price to high-price sedans before multi-link rear suspension became popular in the 1990s. Pure trailing arm has become obsolete as vehicle manufacturers adopted semi-trailing arm. Semi-trailing has a disadvantage that when the wheel moves up and down, camber angle changes, unlike double wishbones suspension. Semi-trailing arm or pure trailing arm suspensions are rigidly attached to the wheels, where more shock and noise could be transferred to the car body, especially under hard cornering or running on bumpy roads. Moreover, a lot of unsprung weight of the trailing arm leads to a decrease in ride quality. Therefore most modern sedans replace it with multi-link or double wishbones suspension. Trailing arm and semi-trailing arms are disappearing from the industry. |
Sub-frame Mounting | Reduction of NVH (Noise, Vibration and Harshness) is a very important issue for modern cars. Conventional suspensions are mounted directly to the chassis (though via rubber bushing), so that NVH can be easily transmitted to the cabin. One popular solution is to mount the suspension onto a sub-frame (still via bushing), which is usually made of aluminum alloy or is produced by hydroforming to minimize the addition of weight. The sub-frame itself can absorb some of the NVH. It is in turn mounted to the body by more bushings, thus reducing NVH further. Today, sub-frame mounting is no longer exclusive for high-price cars. The latest European cars have sub-frame mounting too. |
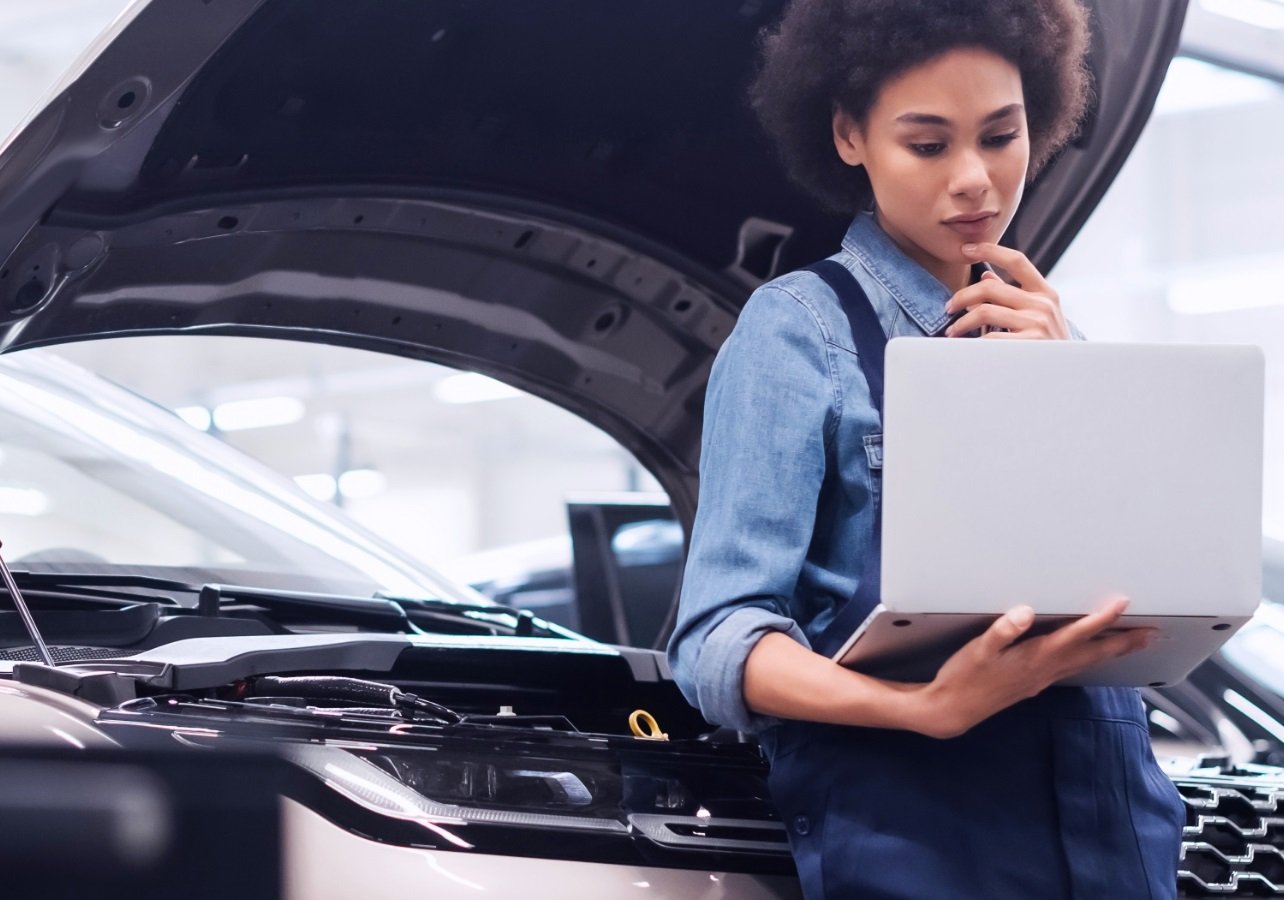
Visit our Technician Library for access to Documents and Downloads
Get in touch
The full Delphi Steering & Suspension product range

Find out where to buy Delphi parts
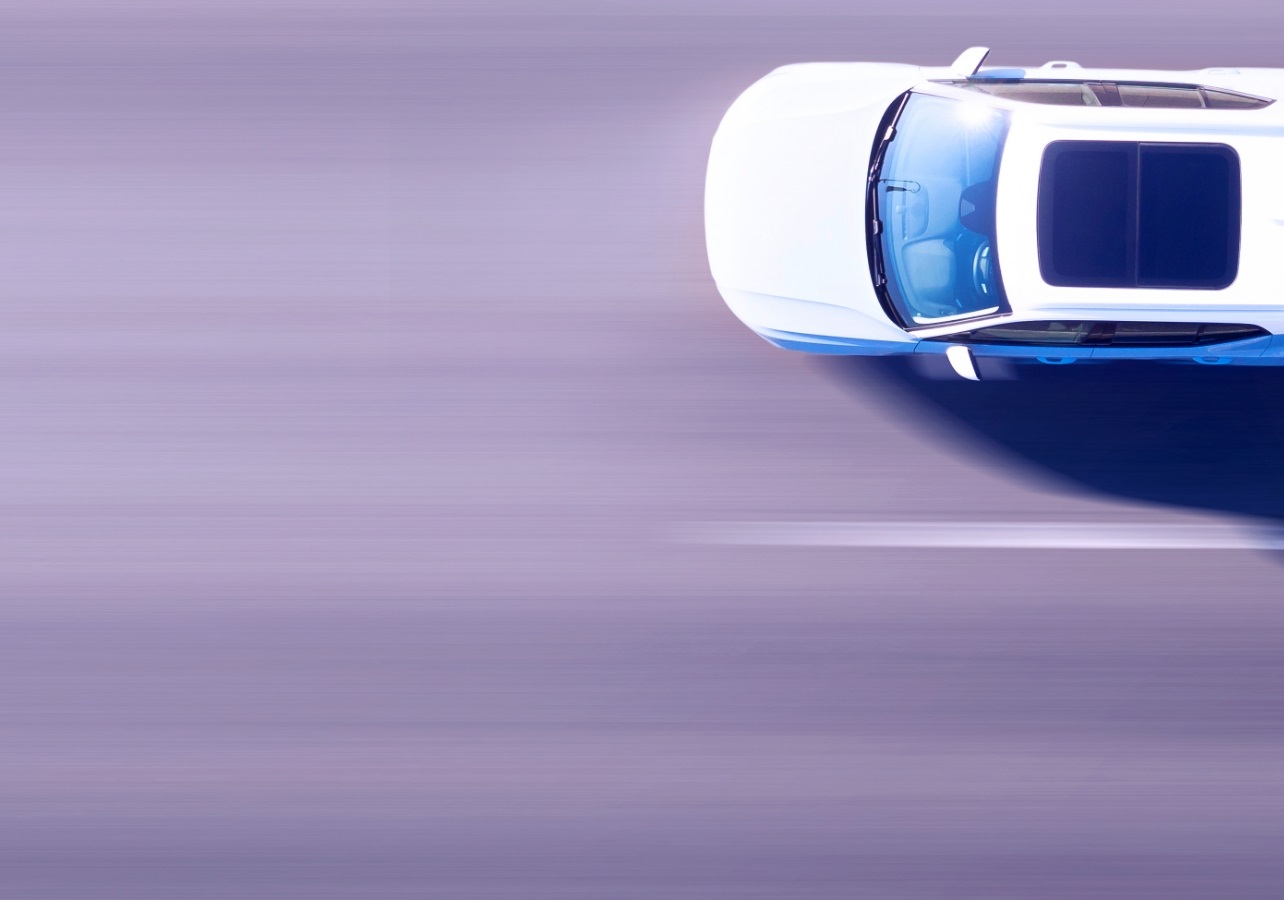