Brake Discs

- Product Information
- Product Resources
- Enquire
- Related Products
ECE R90 certified brake discs
It should come as no surprise that our brake discs for new vehicles launched post 1 st November 2016 are R90 certified, alongside a range for popular older applications. After all, we’ve been meeting these quality standards for many years. The only difference today: our discs now undergo official ECE R90 testing schedules including performance, dynamic friction comparison, high load integrity and thermal fatigue analysis to certify that they perform to a prescribed tolerance of the OE part.
Learn more about Delphi’s R90 certified brake discs and why it matters.

Fully coated brake discs
Thanks to a special zinc-flake, silver Geomet coating, our coated brake discs offer greater and longer-lasting corrosion protection compared with many oil-dipped or partially painted and coated equivalents, whilst also being more cosmetically appealing. And because they have no oil to clean off, they save valuable labour and service time. All this makes for a better protected disc that’s easier to install, easier to dismount as well as being easy on the eye too.

High-carbon brake discs
The added carbon content in our high-carbon discs helps to both reduce the risk of thermal cracking under high-temperature loads, and allows the discs to operate at a cooler temperature, for a more consistent braking performance. It also increases their resistance to distortion or warping for added durability, while delivering noise and judder free braking.
Cross-drilled brake discs
As well as looking cool from behind your wheels, our cross-drilled discs will keep your brakes feeling the same way – cool. The cross-drilled holes dissipate heat, brake dust and gases, helping to keep the pad surface cool and clean and reducing the risk of thermal distortion and warping. These same holes also prevent a film of water forming during wet conditions for improved braked response.

Vented brake discs
Our vented discs feature special internal cooling passages to maximise airflow. By continually moving air across the disc’s surface or through the disc itself, they allow more heat to be dissipated, improving both cooling capacity and resistance to cracking from thermal shock.
Brake discs with bearings
To avoid damage to the bearing during removal, and ensure the correct pressing in into the new, we offer a range of discs with these safety critical components already pre-mounted. They also include both toothed and magnetic ABS sensor rings, as per the OE, and the relevant fixing accessories. All for quick and accurate installation.
One-piece cast iron brake discs
Our one-piece cast iron discs offer an aftermarket alternative to BMW’s patented two-piece bi-metallic composite disc. Engineered from a single piece of cast iron, they deliver the same standards of consistency, longevity and braking performance as the two-piece disc, but at a fraction of the price. And to top it off, they come with fixing screws for quicker and easier fitting.
The Delphi Difference
-
100 years of OE experience, supplier to the world’s top automakers
-
OE heritage and knowledge built into every aftermarket part
-
Comprehensive portfolio for a wide range of vehicles and model years
-
Streamlined SKUs for easy inventory management
-
Support through tools, tips and training
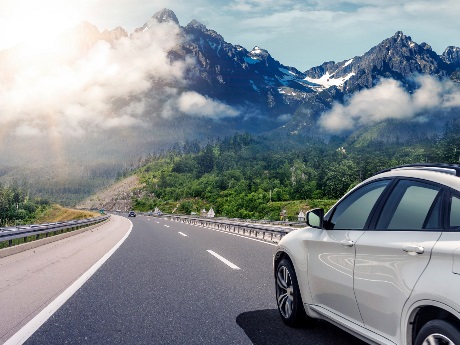
Related product resources and downloads

Resource Highlights
One of the benefits of hybrid and electric vehicles (H/EVs) is their potential to recuperate braking energy, otherwise known as regenerative braking. Here we explain how this energy-efficient system works? And what this means when it comes to servicing them?
What is regenerative braking?
Cast your mind back to school science lessons and you might remember that energy cannot be created or destroyed – it can only change from one form into another. Well the same principle applies to braking. For a car to stop, the kinetic energy built up whilst moving, must go somewhere. In a conventional hydraulic braking system, that means using the friction created between the brake pad and disc, or drum and shoe, to convert the vehicle’s kinetic energy into heat. The heat is then dissipated into the atmosphere and the car slows.
In hybrid and electric cars with regenerative braking, this energy is put to much better use. Instead of simply releasing it into the air, the vehicle turns it into electrical energy, which is stored in the vehicle’s batteries. As well as helping to stop the car, the stored energy provides electricity to the electric motor for future driving, increasing its efficiency.

How does regenerative braking work?
Whilst driving a vehicle with a regenerative braking system, the electric motor draws power from the battery to turn the wheels, creating the kinetic energy it needs to move. When the brakes are applied however, the process switches into reverse mode. Now the kinetic energy that was initially used to propel the vehicle, makes the wheels rotate the electric motor, turning it into a type of generator. Instead of consuming electricity, the motor/generator starts producing it, using the vehicle’s kinetic energy. The electrical energy is then stored in a high voltage battery, where it is used again to help propel the vehicle. Since regenerative braking converts the vehicle’s kinetic energy into electricity, it is also able to slow it too, in the same way hydraulics brake do with friction.
Are HEVS still fitted with a hydraulic braking system?
In most cases, the electric motor/generator will provide sufficient braking power to slow the vehicle. Yet, when it's travelling at high or very low speeds, is stationary or the battery is fully charged, too hot or too cold, the electric motor cannot provide enough braking torque on its own and will need the support of a hydraulic braking system. To what extent will largely depend on the vehicle. For example, on earlier generation Toyota Prius’ (2001-2004), the hydraulic brakes are not used until the vehicle is below seven miles per hour, except for hard stops.
What does this mean for brake service?
Because the hydraulic brakes are essentially a back-up system, they are used less, and in theory should last longer. However, the reality can be very different - with less use, rust and contaminants can quickly build-up, affecting both the disc’s friction surface, the pad mounting, and the caliper piston/slider pins. So, the key braking components still wear - just differently.
Take the caliper carrier as an example. Due to the corrosion from lack of brake use, the brake pads may not be able to fully retract from the disc, causing accelerated, uneven wear. Alternatively, and depending on where the corrosion lies, the pads may not contact the disc properly. As such any corrosion on the disc friction face will not get cleaned off completely, resulting in disc brake pitting as well.
Of course, age, driving conditions and environmental factors such as water, salt spray and temperature changes will all cause wear and tear to the system components. Just like they would on any other vehicle. So, it’s still best practice to perform regular maintenance checks on the entire braking system, whether it’s a hybrid, electric or internal combustion engine powered vehicle – just remember to follow the safety precautions detailed in the vehicle’s manufacturer’s handbook.
To learn about the sophisticated propulsion software and systems inside, visit our Power Electronics category page.
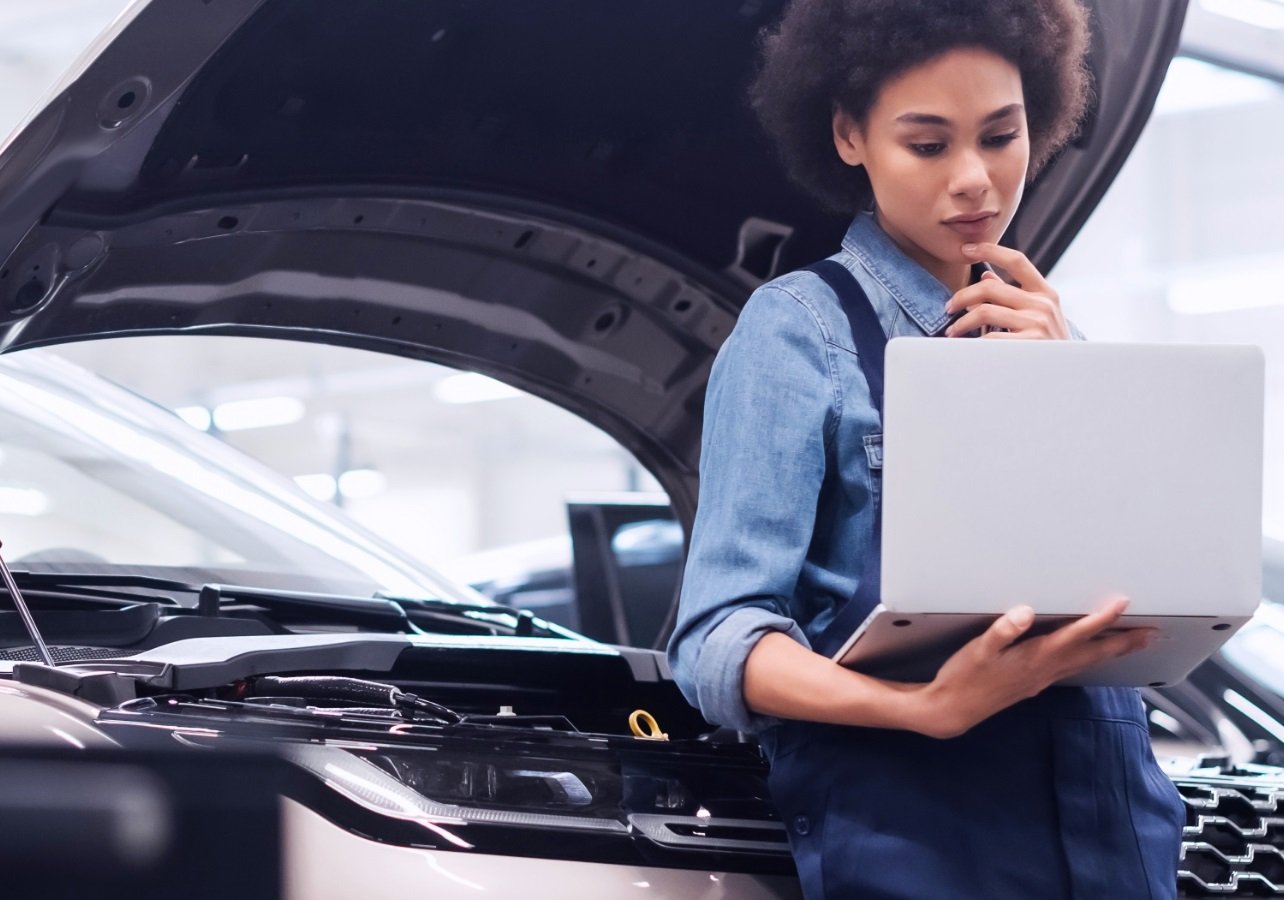
Visit our Technician Library for access to Documents and Downloads
Get in touch
The full Delphi product range

Find out where to buy Delphi parts
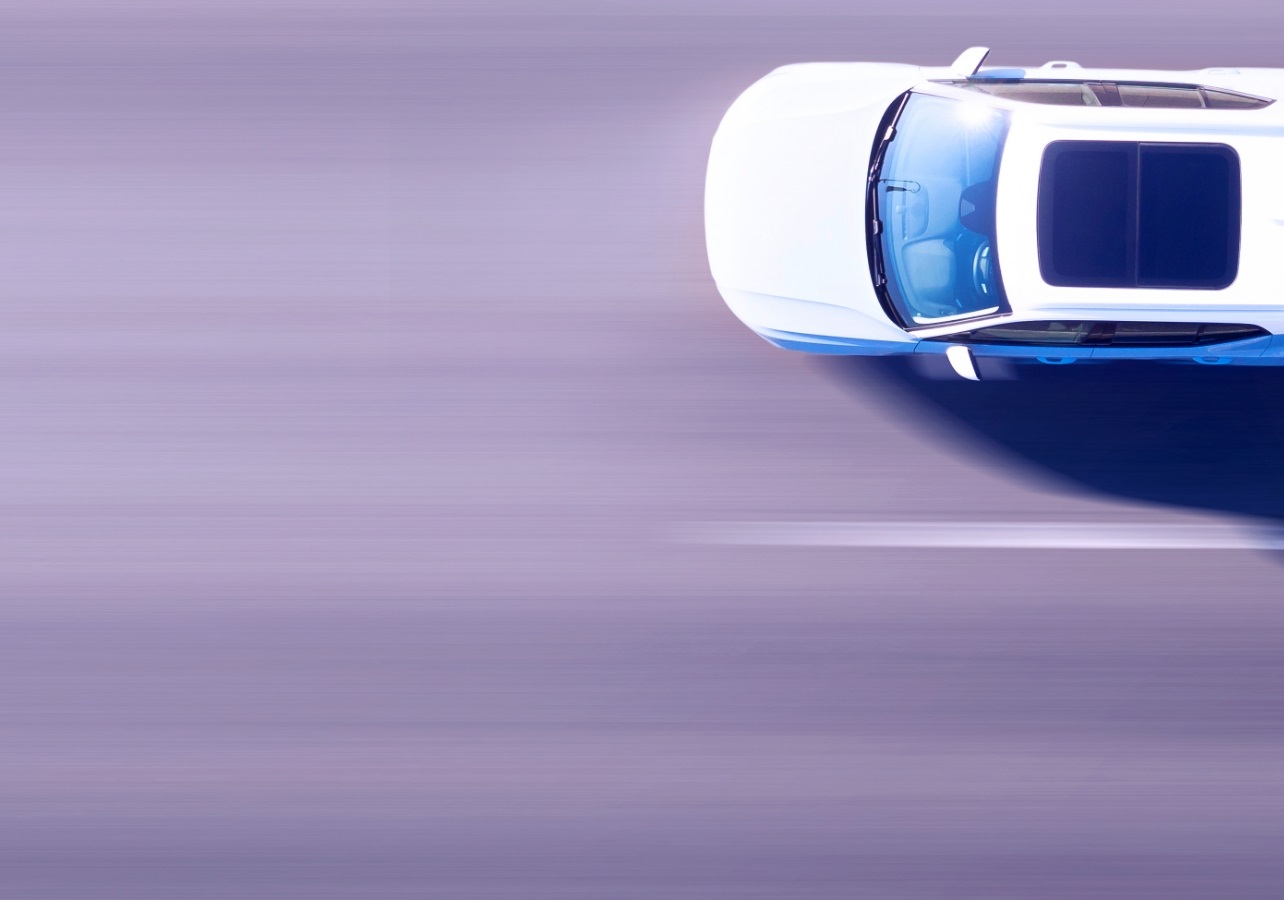