Delphi R90 Brake Discs

- Product Information
- Product Resources
- Enquire
- Related Products
R90 Certified Brake Discs – Quality Counts!
Trust Delphi for OE quality discs
At Delphi, R90 is just a mere formality. As a leading tier-one manufacturer we’ve been meeting R90 quality standards for some time. However, we’ve recently undergone the rigorous testing to confirm that they are indeed R90 compliant, and therefore perform within a prescribed tolerance of the OE parts they are intended to replace. Just like we knew they would.
R90 Certified Brake Discs
Well, take the R90 tests for high load integrity and thermal fatigue as an example. These tests replicate the same stresses the part will be exposed to under every day driving conditions. Such as how well it performs under load. Or how well it withstands prolonged heavy braking compared to the OE part. A substandard part might crack or fracture due to thermal shock, potentially leading to brake failure.
Similarly, dimensional analysis ensures geometric compatibility between the OE and aftermarket disc. If the parts are out of tolerance, even by a small percentage, they may be difficult to install. Worst still you could find your customer returning with complaints about increased noise or judder.
The Delphi Difference
-
100 years of OE experience, supplier to the world’s top automakers
-
OE heritage and knowledge built into every aftermarket part
-
Comprehensive portfolio for a wide range of vehicles and model years
-
Streamlined SKUs for easy inventory management
-
Support through tools, tips and training
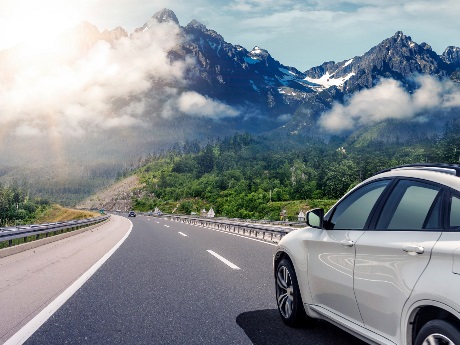
Related product resources and downloads

Resource Highlights
One of the benefits of hybrid and electric vehicles (H/EVs) is their potential to recuperate braking energy, otherwise known as regenerative braking. Here we explain how this energy-efficient system works? And what this means when it comes to servicing them?
What is regenerative braking?
Cast your mind back to school science lessons and you might remember that energy cannot be created or destroyed – it can only change from one form into another. Well the same principle applies to braking. For a car to stop, the kinetic energy built up whilst moving, must go somewhere. In a conventional hydraulic braking system, that means using the friction created between the brake pad and disc, or drum and shoe, to convert the vehicle’s kinetic energy into heat. The heat is then dissipated into the atmosphere and the car slows.
In hybrid and electric cars with regenerative braking, this energy is put to much better use. Instead of simply releasing it into the air, the vehicle turns it into electrical energy, which is stored in the vehicle’s batteries. As well as helping to stop the car, the stored energy provides electricity to the electric motor for future driving, increasing its efficiency.

How does regenerative braking work?
Whilst driving a vehicle with a regenerative braking system, the electric motor draws power from the battery to turn the wheels, creating the kinetic energy it needs to move. When the brakes are applied however, the process switches into reverse mode. Now the kinetic energy that was initially used to propel the vehicle, makes the wheels rotate the electric motor, turning it into a type of generator. Instead of consuming electricity, the motor/generator starts producing it, using the vehicle’s kinetic energy. The electrical energy is then stored in a high voltage battery, where it is used again to help propel the vehicle. Since regenerative braking converts the vehicle’s kinetic energy into electricity, it is also able to slow it too, in the same way hydraulics brake do with friction.
Are HEVS still fitted with a hydraulic braking system?
In most cases, the electric motor/generator will provide sufficient braking power to slow the vehicle. Yet, when it's travelling at high or very low speeds, is stationary or the battery is fully charged, too hot or too cold, the electric motor cannot provide enough braking torque on its own and will need the support of a hydraulic braking system. To what extent will largely depend on the vehicle. For example, on earlier generation Toyota Prius’ (2001-2004), the hydraulic brakes are not used until the vehicle is below seven miles per hour, except for hard stops.
What does this mean for brake service?
Because the hydraulic brakes are essentially a back-up system, they are used less, and in theory should last longer. However, the reality can be very different - with less use, rust and contaminants can quickly build-up, affecting both the disc’s friction surface, the pad mounting, and the caliper piston/slider pins. So, the key braking components still wear - just differently.
Take the caliper carrier as an example. Due to the corrosion from lack of brake use, the brake pads may not be able to fully retract from the disc, causing accelerated, uneven wear. Alternatively, and depending on where the corrosion lies, the pads may not contact the disc properly. As such any corrosion on the disc friction face will not get cleaned off completely, resulting in disc brake pitting as well.
Of course, age, driving conditions and environmental factors such as water, salt spray and temperature changes will all cause wear and tear to the system components. Just like they would on any other vehicle. So, it’s still best practice to perform regular maintenance checks on the entire braking system, whether it’s a hybrid, electric or internal combustion engine powered vehicle – just remember to follow the safety precautions detailed in the vehicle’s manufacturer’s handbook.
To learn about the sophisticated propulsion software and systems inside, visit our Power Electronics category page.
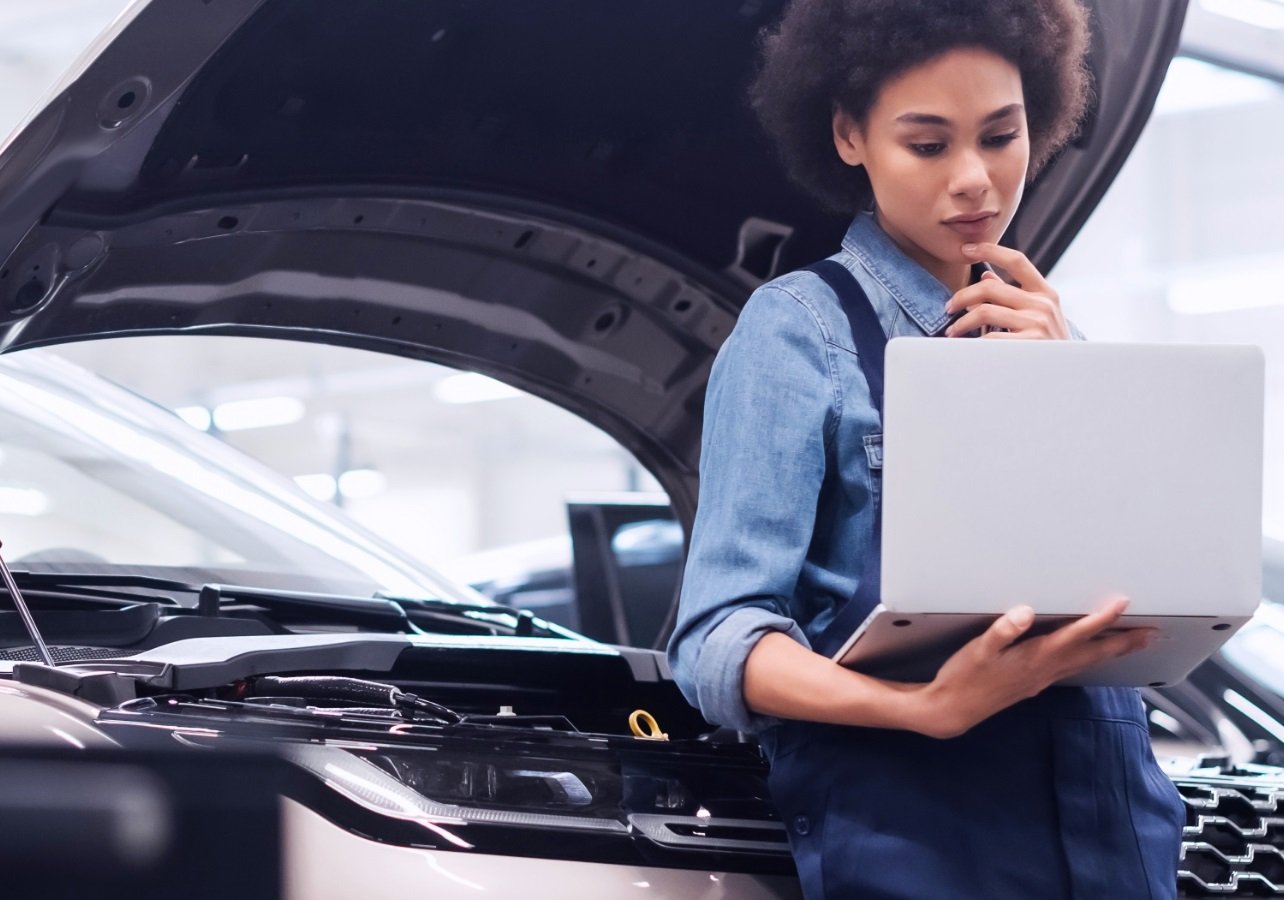
Visit our Technician Library for access to Documents and Downloads
Get in touch
The full Delphi Brake Discs product range

Find out where to buy Delphi parts
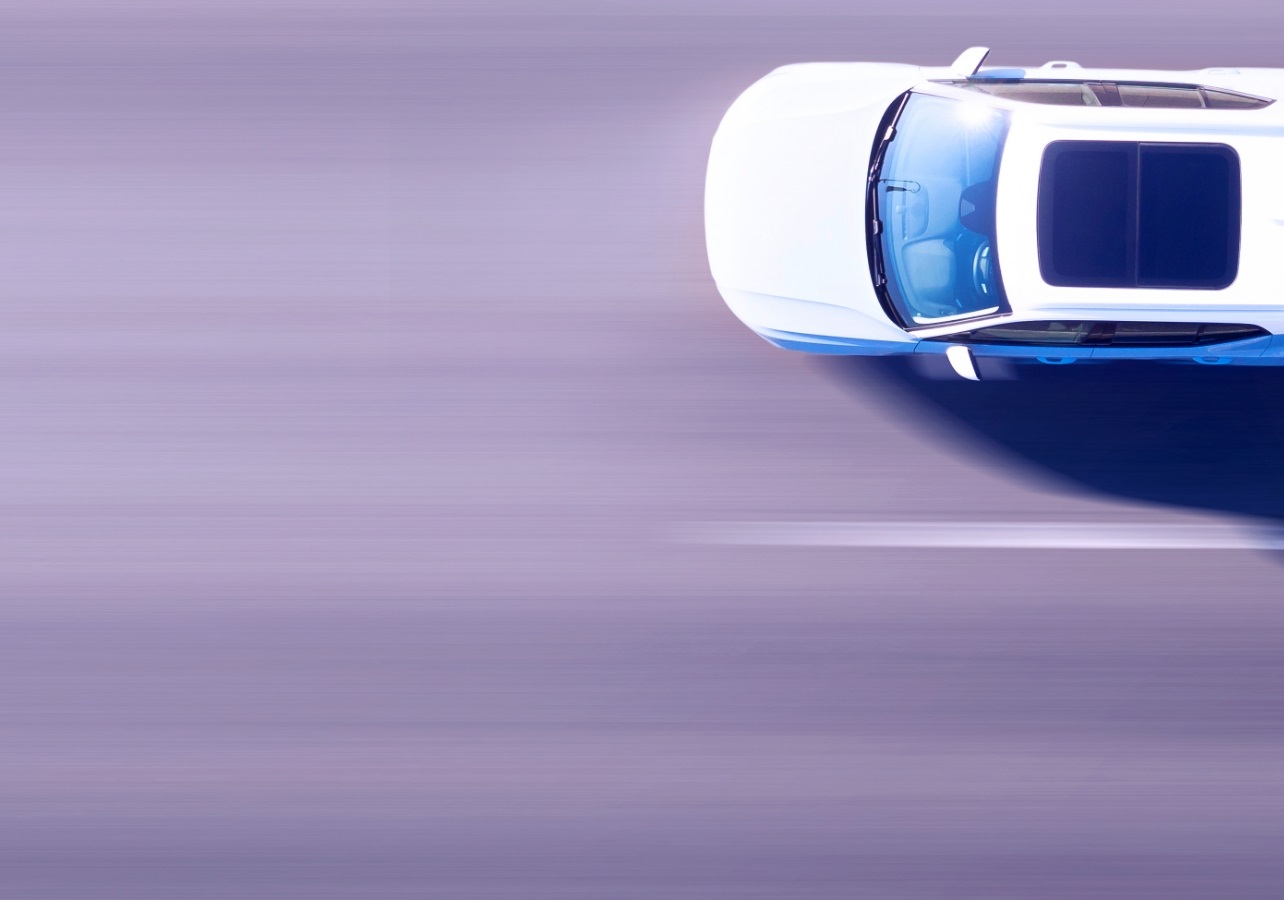