Resource Highlights
In this article you will find out about our Steering & Suspension Quality Test Results.
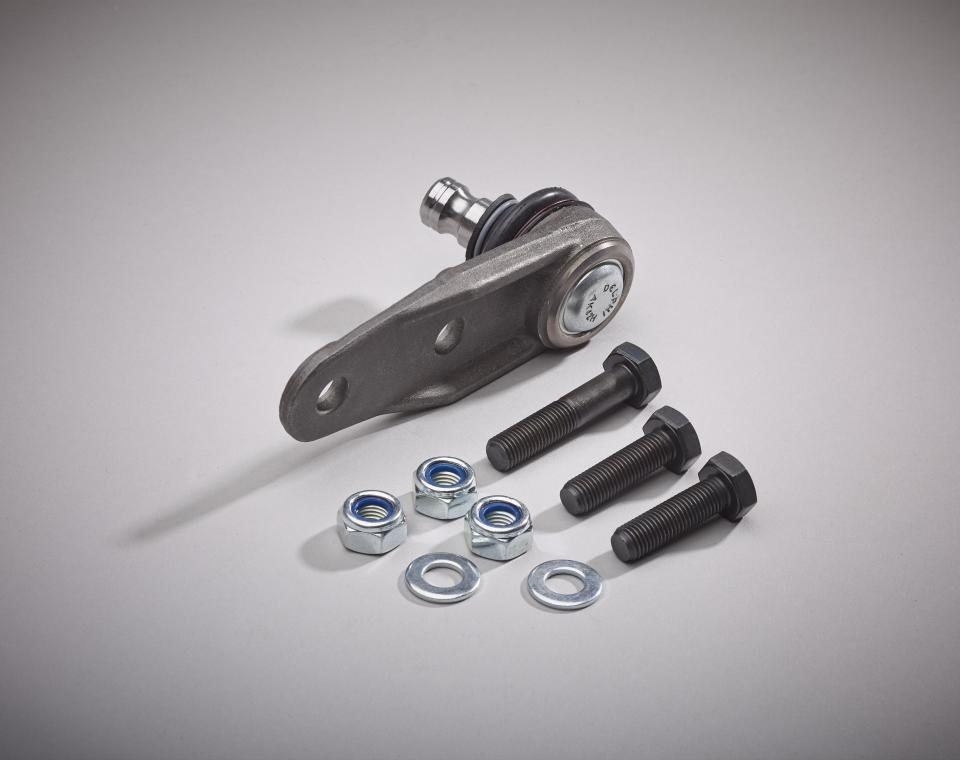
- Ball-pin rotational and break-away torque test
The rotational test measures the force required to rotate the ball-pin within the housing and validates the smooth movement of the steering joint. The break-away test measures the force required to move the ball-pin when the steering wheel turns. Delphi matched the OE part in both torque tests. The competitors ranged from below the accepted range to four times the torque required. With higher torque values than the OE, steering can be stiff and difficult to self center after turning, rendering the vehicle unpredictable. If less than the OE, the steering could feel loose and unstable.
- Ball joint push out test
Measures the force required to push out/remove the ball-pin from the housing. It is an important safety check to ensure the part can withstand forces applied to the vehicle suspension system in real road conditions. If the force required to push the ball-pin out from its housing is below the OE requirements, there is a risk the joint could fail. Delphi performed within the one percent tolerance required.
- Ball-pin angular movement test
If the ball-pin angular movement is lower than the OE specification, it could restrict the movement of the steering or the suspension, causing excessive stress on other system components and leading to premature failure of the parts. In this test, Delphi matched the OE specifications.
- Ball joint pull out test
Measures the force required to pull the ball-pin out from the housing. If the force required to remove the ball-pin is below the OE spec, there is a risk the joint could fail during normal driving conditions causing the vehicle to lose directional control, as the wheel hub would no longer be anchored to the suspension arm. Again, Delphi performed within one percent required of the OE specs.
- Link stabilizer tensile strength test
Validates the product housing and welding strength by applying force through the center of the housing until breakage occurs. Breakage should not happen at the points where the bar is welded to the housing. If the tensile strength of a link stabilizer is below the OE, there is a risk of premature failure resulting in vehicle instability and a knocking noise when driving the vehicle. Due to Delphi’s welding process and material specification, the link stabilizer performed to OE specifications.
- Rubber to metal durability test
Confirms the integrity of the part design and manufacturing process used to make it. After 220,000 test cycles, the Delphi bush remained intact with a small amount of rubber cracking. In contrast, one competitor suffered a complete failure of the bonding in less than 30,000 cycles. This can result in the failure of the component assembly into which it is installed.
Delphi steering and suspension parts quality test results
As part of its commitment to maintaining OE integrity on every one of its parts, Delphi recently conducted quality test results on its steering and suspension parts together against original equipment and key European competitor parts. Measuring for torque, movement, durability and strength integrity, tests were performed on ball joints and link stabilizers with Delphi matching or remaining within tolerance of OE specifications, while competitor results varied.
Delphi engineers carry out dimensional analysis to ensure geometric compatibility between the OE and aftermarket product, together with stringent analysis of the chemical composition and mechanical properties of the materials used. Further product testing is employed during the manufacturing process including material and dimensional checks, crack detection, and corrosion testing.
All Delphi parts produced adhere to its global technical requirements, whether destined for OE manufacturers or aftermarket customers. All parts released for the aftermarket undergo the same rigorous product development processes, including Production Part Verification (PPV) and Production Part Approval Process (PPAP). The purpose of PPV is to confirm the part being produced performs exactly as the prototype was designed, and the purpose of the PPAP is to ensure every part meets all of the requirements defined in the engineering samples. For example, the steering and suspension ball joint tests specifically focused on strength and durability performance. Both are critical to provide drivers a safer diving experience.
SIGN UP TO FIND MORE
Fill yp your details to hear more from our experts and get the latest updates from Delphi.